Our team at Dockwa is stoked to be collaborating with the Salty Dawgs Sailing Association (SDSA) to share monthly cruising tales in The...
Can a Boat Lithium Upgrade be a DIY Project?
Post by Salty Dawg Sailing Association - Published on 04/01/25 4:00 AM
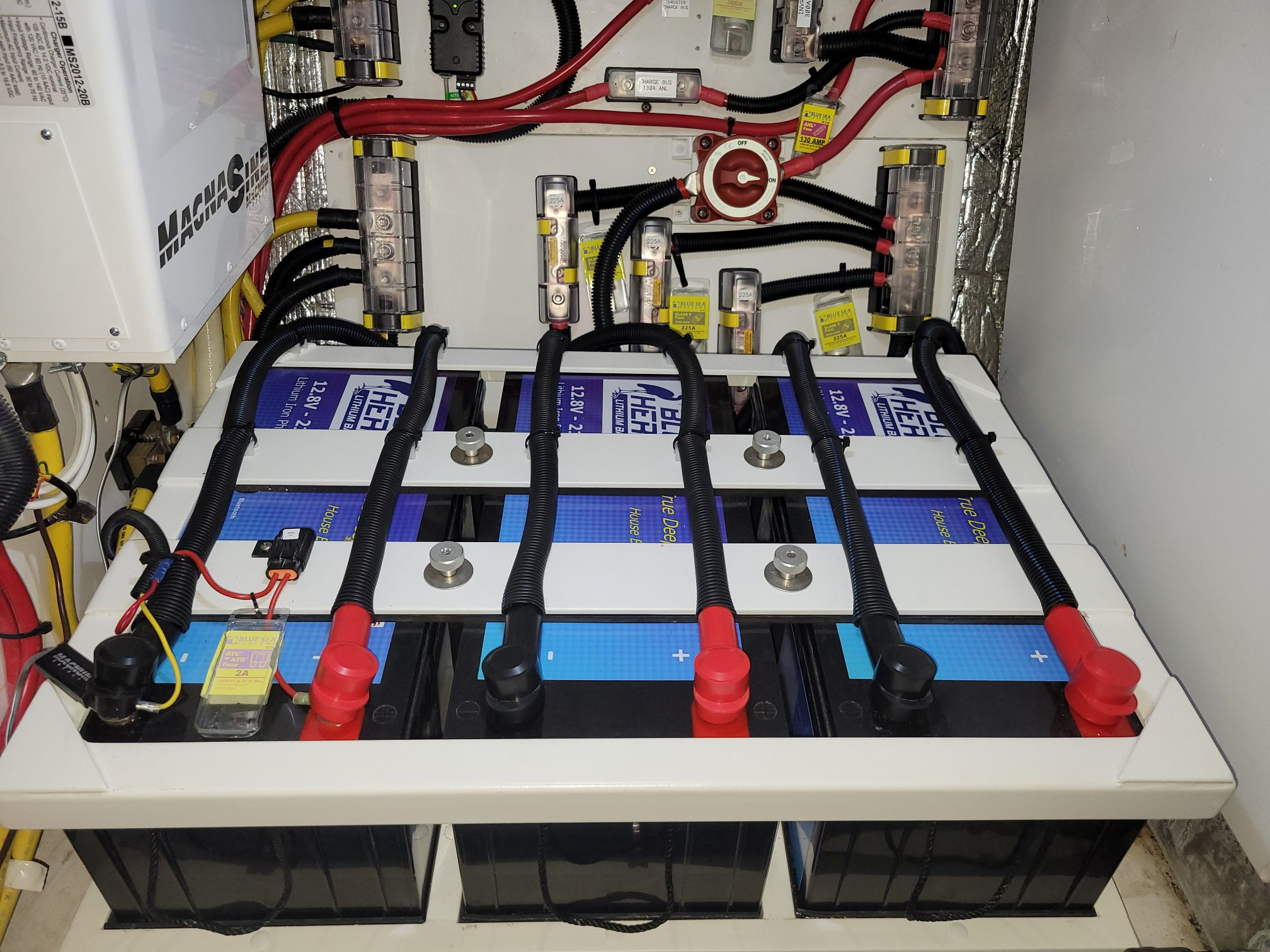
For cruisers chasing self-sufficiency and long days off the grid, upgrading to lithium batteries is one of the most talked-about projects on the dock. But with all the buzz comes a big question: can you tackle a lithium upgrade yourself? In this piece, long-time sailor, engineer, and lithium expert Hank George breaks down the realities of DIY lithium installations. From battery bank sizing and alternator considerations to safety tips and trusted manufacturers, this is a must-read for anyone eyeing a more efficient, reliable power setup aboard.
Can a Boat Lithium Upgrade be a DIY Project?
by Hank George
Lithium batteries have been on the market for nearly 20 years now. Beta-testing was done in those early years, over 10-thousand research papers and studies have been completed, and in particular, lithium iron phosphate (LiFePO4 or LFP for short) batteries have now become the standard for marine, RV and solar battery bank installations. Other types of Lithium=ion batteries with Cobalt and nickel constituents are less safe and have the potential for auto-ignition and explosion. So, with that body of knowledge and demonstrated safety, is it plausible to build one’s own battery bank and install the lithium batteries in one’s boat? I’ll try to touch on the relevant issues that question introduces. This article focuses on use of Lithium Iron Phosphate (LiFePO4) batteries.
1. Can I Build a Safe and Reliable Lithium Battery Myself?
While one can find the components to build your own lithium battery, using online offered lithium cells, empty battery cases, and BMS units, building your own batteries is not an area for a reliable DIY project. There is much more to a battery than just sticking parts together. Cells that can be bought on-line range from ones that are used and may only last a few months, to reject cells that may only last a year or two. BMS’s may have only limited margin between design limits and maximum loads the battery may experience. DIY folks don’t have access to independent QC inspection services used by US companies before releasing products from China for delivery to the US. So, my advice is not to try to build your own batteries – there is too much that can go wrong.
2. Should I Buy from a Reputable US Company? (Or just buy low-cost Chinese-direct batteries off Temu or Amazon?)
As noted above, US companies use independent QC services to inspect products, like assembled batteries or components from a listed, billion-dollar company to ensure the high quality and long-life US customers will demand. Batteries by these companies are rigorously tested by UL and in-house test labs. US battery companies would not even consider the low-cost Chinese-direct batteries to offer to their customers and dealers. So, for the purchase of batteries I would highly recommend sticking with products from reputable US battery companies.
3. Battery Bank Sizing
For those thinking of installing a lithium battery bank themselves, a good start on battery bank sizing is to consider the usable AH of their lead acid battery bank (i.e., 50% of rated Ah) and going at least 20% above that in a lithium battery bank. And go even higher if planning to add more loads like Starlink, running air conditioning or powering an induction hot plate. Or maybe you need even more capacity, such as to support 24 hours of passage-making or gaining independence to anchor out rather than typing-up in a marina. I have seen boats with 400Ah for a small cruising boat to 600Ah to 900Ah in a larger boat do just fine, and others that needed 2,000Ah to 3,600Ah at 12V due to larger needs.
4. Cables, Fuses, Existing DC Distribution System
Suggestions here:
- Be sure to size battery cables based on ABYC guidelines and have them made by qualified sources. BatteryCablesUSA.com is an excellent source of made-to-order cables. This is not an area to cut corners, as high current through improperly prepared cables can lead to an electrical fire.
- Add fusing per ABYC recommendations. This means a fuse at the output of each lithium battery, and these are to be Class T fuses unless manufacturer established short circuit maximum current can be accommodated by an MRBF fuse and then place a Class T fuse at the battery bank combined output.
- Exiting DC Distribution circuits on older boats are prime for high resistance electrical issues due to corrosion, loose connections, and undersized cables. These are the main culprits that lead to a boat fire. When doing a lithium upgrade it is the prime opportunity to check for any of these issues. I highly recommend engaging an ABYC certified technician or marine surveyor to check your system for any of these conditions, including opening enclosures. This is money well spent!
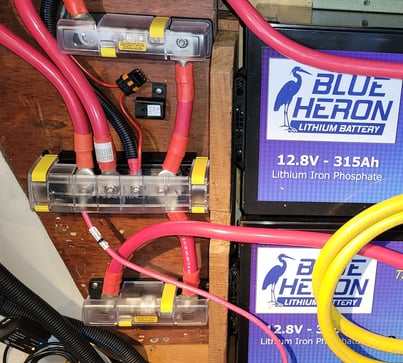
4. Alternator Issues to Consider
Alternators charging into a lithium battery present three issues that need to be addressed.
- One is the charge voltage in a standard alternator are not good for lithium; generally, much higher and held for a longer duration than desired for lithium. This can be addressed by:
- Converting to an externally regulated alternator, with proper settings for lithium, to charge directly into the lithium bank. This is the desired approach as it supplies much more power than can be harvested by a DC-DC Charger. But, other factors then need to be properly addressed as noted below.
- Leaving the stock alternator charging the start battery, and adding a DC-DC Charger to harvest some of the alternator energy to charge the House Bank. To avoid short cycling, the DC-DC should be sized at 40% of the alternator rating, or less.
- Another issue when charging lithium with an alternator is the potential for alternator over-heating, as lithium has such low internal resistance compared to lead acid. The alternator will put out 120% of their rating. One can accommodate this by depowering the alternator using the external regulator and performing a careful check and test – best carried out by a qualified marine electrician, with input from the battery manufacturer. Then as an added level of safety, install an alternator temperature sensor feeding into the external regulator, in case temps get higher than expected in the general installation. Do not rely solely on this sensor to address this issue.
- The third issue is the potential for damaging alternator diodes in a load dump, if you were to have some incident that caused all BMS units to isolate charging flow to the batteries. The are various methods to address this issue, such as adding a Balmar Alternator Protection Module (APM), installing a Wakespeed regulator with communications from the BMS units, and adding a lead acid battery fed through an isolator. Each of these options have avid proponents. I won’t get into recommendations in this article, but you should do at least one of these.
6. Chargers
Charging devices such as Battery Chargers, Inverter/Chargers, MPPT Controllers, and DC-DC Chargers, need to have their charging profile settings adjusted to the battery manufacturer’s recommendations. If the charging device cannot be adjusted to meet the desired charge profile, it should be replaced. Working with a skilled technician and a reputable battery manufacturer can facilitate this step.
7. Battery Monitors
With lithium one can no longer rely just on a voltmeter to get a sense of their State of Charge (SoC). A quality battery monitor with a shunt, such as a Victron BMV-712 set up correctly, will give good results. Estimating routines built into a BSM and observed through Bluetooth should only be a fallback. The BMS is accurate for its safety functions, but not able to address the more complex determination of SoC.
7. Technical Support
A reputable battery manufacturer should have engineering support readily available. And better would be one with experienced sailors and cruisers on staff.
8. Installation Testing and Inspection
A key step after a lithium upgrade, before trying to charge batteries or power loads, is a comprehensive inspection and testing regimen by a qualified person (I strongly suggest an ABYC technician looking at all the DIY work you did.) Checking cable sizing, soundness of crimp fittings, fuse sizing, batteries being secured, checking for the conditions noted in #4 above, and checking temperatures at connection points, bus bars, fuses, battery surfaces, and battery terminals when charging with a large current should all be part of this last step.
About the Author – Hank is a degreed engineer and life-long sailor. He served on the Salty Dawg Sailing Association Board, and as President. He became involved in lithium battery applications on boats in its infancy 15 years ago, has managed or performed numerous lithium upgrades, conducted many webinars on the subject, and is the founder and owner of Blue Heron Lithium Battery located in Virginia.
Be the first to access boater stories like this one by subscribing to our new newsletters,The Running Fix and Dock Talk!